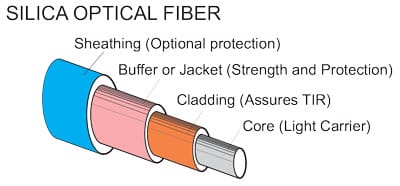
Step index silica optical fibers are made from a synthetic silica core and a cladding material with a lower index of refraction than the core. This combination assures the clad contains light within the core and allows that light to travel at many different angles through the core.
Step index silica optical fibers are typically divided into three main categories:
- Silica/Silica (Si/SI)
- Polymer Clad Silica (PCS)
- Hard Polymer Clad Silica (HPCS).
In addition to the fiber, a buffer (also known as a coating) and sometimes an additional jacketing (also known as sheathing) are part of the fiber makeup. Coating provides the protective strength characteristic of all fibers. Without a coating, silica fibers are brittle and prone to scratching and breakage.
Each fiber category and their associated coating offerings are described below:
Silica/Silica (Si/Si)
Silica/silica fibers (available in .12, .22, .37 NA) are commonly referred to as fused doped silica (FDS) fibers. FDS fibers have a fused silica core, a cladding layer of doped silica, and one or more layers of a coating. Coating materials are applied to the optical fiber as the fiber is drawn on the draw tower. Below are several common coating materials for FDS fibers:
Polyimide
Polyimide is the most common coating for FDS fibers. It’s a very strong material with an operating range of -190°C to roughly 375°C (-310°F to 707°F).
Polyimide coatings are high temperature thermally cured to optical fibers in recurring layers of 3 to 5 microns thickness at a time. There are typically applied in 2 to 5 layers. Because of the close bonding to the fiber, polyimide coatings cannot be removed mechanically — plasma or chemical processes are required. This characteristic makes them ideal for gathering and forming large area “bundles” with high packing factor for a variety of scientific applications.
Polyimide coatings are Class VI biocompatible and are typically used on fibers between 35 and 600 microns in diameter.
Polyimide coated fibers are always selected to manufacture bundle assemblies as well as single assemblies. Polyimide coatings are also best suited to harsh environment (high temperature, vacuum, and high pressure) applications due to their very large temperature range and extremely low outgassing characteristic. Polyimide coatings are not suited to fibers larger than 600 microns in diameter, as the strong interface it creates actually induces physical stress in larger fibers.
Acrylate
Acrylate has an operating temperature of -40°C to 85°C (-40°F to 185°F). It is suitable for room temperature environments without extreme temperature, vacuum, or pressure requirements. Acrylate coating has Class VI biocompatibility rating.
Because Acrylate coating strips easily and cleanly, the coating is selected most often to manufacture single fiber assemblies. Acrylate coated fibers are usually selected to manufacture single fiber assemblies, but if the Acrylate coating is thin, it can also be used for making bundle assemblies. Acrylate is most commonly used on fibers between 50 and 1,000 microns in diameters and is applied in one layer between 10 and 100 microns in thickness.
Nylon with silicone
Nylon is a durable material with an operating range of -40°C to 100°C (-40°F to 212°F). A thin layer of silicone is required between the nylon and fiber cladding in to affix the nylon to the fiber.
Nylon coated fibers are usually selected to manufacture single fiber assemblies. Nylon coatings are easily stripped but may require a second cleaning step to ensure complete removal of the silicone layer. Like Acrylate, Nylon coating has a Class VI biocompatibility. Unlike Acrylate, the silicone layer prevents the use of this fiber to manufacture bundle assemblies.
Nylon is most commonly used on fibers between 200 and 2,000 microns in diameter and is applied in one layer between 100 and 200 microns in thickness.
Ethylene-tetrafluoroethylene with silicone
Ethylene-tetrafluoroethylene is more commonly known as ETFE or by the trade name Tefzel©.
It is a strong material with an operating range of -40°C to 150°C (-40°F to 302°F). A thin layer of silicone is required between the ETFE and fiber cladding in order to affix the ETFE. This coating is selected when manufacturing single fiber assemblies which require higher heat resistance (compared to Nylon and Acrylate). Like Nylon, ETFE coatings are easily stripped, but could require a second cleaning step to ensure complete removal of the silicone layer. This coating also has a Class VI biocompatibility rating.
Unlike Acrylate, the silicone layer prevents the use of this fiber in manufacturing bundle assemblies.
ETFE is most commonly used on fibers between 200 and 2,000 microns in diameter and is applied in one layer between 100 and 200 microns in thickness.
Polymer Clad Silica (PCS)
PCS fibers have a fused silica core and silicone cladding and one layer of a coating. The NA of these fibers are length dependent. It is 0.40 for shorter lengths around 2 meters and 0.30 for lengths around 40 meters. PCS fibers are a lot cheaper than Silica/Silica fibers but can be challenging to use due to pistoning issues, which may occur if the fiber is bent too much. Coating materials are applied to the optical fiber as the fiber is drawn on the draw tower. Below are several common coating materials for PCS fibers:
Acrylate
Acrylate has an operating temperature of -40°C to 85°C (-40°F to 185°F). It is suitable for room temperature environments without extreme temperature, vacuum, or pressure requirements. Acrylate coating has Class VI biocompatibility rating.
Because Acrylate coating strips easily and cleanly, the coating is selected most often to manufacture single fiber assemblies. If applied thinly, Acrylate can also be used for making bundle assemblies. Acrylate is most commonly used on fibers between 50 and 1,000 microns in diameters and is applied in one layer between 10 and 100 microns in thickness.
Nylon with silicone
Nylon is a durable material with an operating range of -40°C to 100°C (-40°F to 212°F). A thin layer of silicone is required between the nylon and fiber cladding to affix the nylon to the fiber.
Nylon coated fibers are usually selected to manufacture single fiber assemblies. Nylon coatings are easily stripped but may require a second cleaning step to ensure complete removal of the silicone layer. Like Acrylate, Nylon coating has a Class VI biocompatibility. Unlike Acrylate, the silicone layer prevents the use of this fiber to manufacture bundle assemblies.
Nylon is most commonly used on fibers between 200 and 2,000 microns in diameter and is applied in one layer between 100 and 200 microns in thickness.
Ethylene-tetrafluoroethylene with silicone
Ethylene-tetrafluoroethylene is more commonly known as ETFE or by the trade name Tefzel©.
It is a strong material with an operating range of -40°C to 150°C (-40°F to 302°F). A thin layer of silicone is required between the ETFE and fiber cladding in order to affix the ETFE. This coating is selected when manufacturing single fiber assemblies where higher heat resistance (compared to Nylon and Acrylate) is required. Like Nylon, ETFE coatings are easily stripped, but could require a second cleaning step to ensure complete removal of the silicone layer. This coating also has a Class VI biocompatibility rating.
Unlike Acrylate, the silicone layer prevents the use of this fiber to manufacture bundle assemblies.
ETFE is most commonly used on fibers between 200 and 2,000 microns in diameter and is applied in one layer between 100 and 200 microns in thickness.
Hard Clad Silica
Hard clad silica (HCS) (available in .37 and .48 NA only) is also commonly referred to as Hard Polymer Clad silica (HPCS).
HCS fibers tend to be less expensive than FDS fibers. They also tend to underperform FDS fibers in temperature, transmission, performance, and durability. HPCS fibers feature a fused silica core, hard polymer cladding, and generally a single layer of coating. Coating materials are applied to the optical fiber as the fiber is drawn on the draw tower. Below are common HCS coating materials.
Nylon with silicone
Nylon is a durable material with an operating range of -40°C to 100°C (-40°F to 212°F). A thin layer of silicone is required between the nylon and fiber cladding in to affix the nylon to the fiber.
Nylon coated fibers are usually selected to manufacture single fiber assemblies. Nylon coatings are easily stripped but may require a second cleaning step to ensure complete removal of the silicone layer. Like Acrylate, Nylon coating has a Class VI biocompatibility. Unlike Acrylate, the silicone layer prevents the use of this fiber to manufacture bundle assemblies.
Nylon is most commonly used on fibers between 200 and 2,000 microns in diameter and is applied in one layer between 100 and 200 microns in thickness.
Ethylene-tetrafluoroethylene with silicone
Ethylene-tetrafluoroethylene is more commonly known as ETFE or by the trade name Tefzel©.
It is a strong material with an operating range of -40°C to 150°C (-40°F to 302°F). A thin layer of silicone is required between the ETFE and fiber cladding in order to affix the ETFE. This coating is selected when manufacturing single fiber assemblies where higher heat resistance (compared to Nylon and Acrylate) is required. Like Nylon, ETFE coatings are easily stripped, but could require a second cleaning step to ensure complete removal of the silicone layer. This coating also has a Class VI biocompatibility rating.
Unlike Acrylate, the silicone layer prevents the use of this fiber to manufacture bundle assemblies.
ETFE is most commonly used on fibers between 200 and 2,000 microns in diameter and is applied in one layer between 100 and 200 microns in thickness.
Type of Fiber | Single Assembly? | Bundle Assembly? | Bond Strength | Pull Strength | Proof Test Level | Underwater applications | Deep UV application | Solarization | Wavelength Range(nm) | Relative Cost | Numerical Aperture (NA) | Maximum Temperature (C) |
---|---|---|---|---|---|---|---|---|---|---|---|---|
Si/Si (FDS) | YES | YES | Very Strong | Very Strong | 60 to 100 KPSI | YES | YES | YES - Low Solarization is avilable | 193nm to 2,500nm | $$$ | 0.22 as Standard, but readily available in 0.12, 0.28 and even 0.37 | -190 to +375 Degrees C |
PCS | YES | NO | Medium | Medium | 60 to 80 KPSI | No | No | No | 350-2,200 | $ | Length dependent from 0.30 to 0.40 | -40 to +150 Degrees C |
HPCS | YES | NO | Strong | Strong | 60 to 100 KPSI | YES | No | NO | 400-2200 | $$ | 0.37 or 0.48 | -40 to + 150 degrees C |
For All 3 Types – Minimum Bend Radius (Short Term): 100X clad radius, Minimum Bend Radius (Long Term): 300X clad radius