For general consideration, there are two fiber types: Multimode step index fibers, and single mode graded index fibers. We specialize in multimode, step index fibers. Multimode Step index fibers have a consistent core density, and propagate light using the principles of TIR (total internal reflection)
Our fibers are composed of two distinct and different types of optically conducting material. For simplicity, the term glass will be used for all types of fiber.
The center, or CORE of the fiber is the portion that actually carries light.
A thin layer of glass with a lower index of refraction, called the CLAD, surrounds the core and is fused to it, creating a totally reflecting barrier at the interface of the glasses. The clad also keeps extraneous light from entering the core. (Operating in air)
Our typical glass fiber, used for most general light carrying applications, will be .001 to .003 inches (25-75 microns) in diameter. It will have 83% of its area composed of core and 17% of the area will be clad. We can manufacture any fiber diameter your application calls for. Once a fiber diameter exceeds 400um, we would call the fiber a rod, because this diameter is not very flexible.
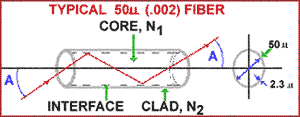
DIFFERENT MATERIALS
Optical fibers are commonly produced from glass, plastic and synthetically fused silica, often called silica or quartz fiber. Each type has its own advantages and drawbacks. For data communication applications, silica fiber is the overwhelming choice. For illumination and sensing applications, glass fiber is probably a better choice for cost and acceptance angle considerations, while plastic excels for ease of assembly in applications that do not require operating temperatures above 175 degrees F. (70°C).
When the same glass core is matched with different clad material(s), the numerical aperture of the resulting fiber is effected, which in turn, changes the fiber’s acceptance angle.
BUFFER
Some fiber types require a buffer. A buffer is a synthetic coating added to the clad. It’s applied to the fiber as it leaves the furnace. The function of the buffer is to protect the fiber from scratching, which will cause a break. Silica fiber requires a buffer, typically made from Polyimide, silicone or acrylate materials. Once the buffer is applied, silica fibers become very strong, and are often proof tested to 1000’s of PSI. The most common silica fiber we use has a polyimide buffer; it’s strongest and offers the highest temperature resistance.
The optical fibers we draw do not require a buffer; they are almost as strong a silica fibers. Because they require no buffer, the number of cores in a bundle is higher, resulting in a bundle construction with lower packing losses.
Plastic fibers do not require a buffer. Their cladding area is the smallest of the fibers we use, so a bundle made from plastic fibers will exhibit the lowest packing loss (Assuming all fibers types are packed to the same percentage of ferrule area). For the same reason, plastic fibers scratch (and leak) easily; they have a low PSI pull test value.
TRANSMISSION
The lowest transmission loss fiber we offer is silica fiber.
Transmission efficiency is good in the range of 200nm – 2.1um
Plastic fiber has better transmission than leaded glass in the shorter wavelengths, but is limited to 400nm – 700nm.
The next best performing fiber is leaded glass. Transmission range for 390nm-1.6um
Sometimes it’s important to know how many fibers there are in a bundle diameter. Try our fiber count calculator below: